3D Concrete Printing FAQs
Get answers to the basics of 3D construction concrete printing, as well as X-Hab 3D printers, materials, and more.
Search 3D Concrete Printing FAQs by Category
There are still plenty of questions surrounding the emerging technology of 3D concrete printing. Look below for the category that piques your interest you.
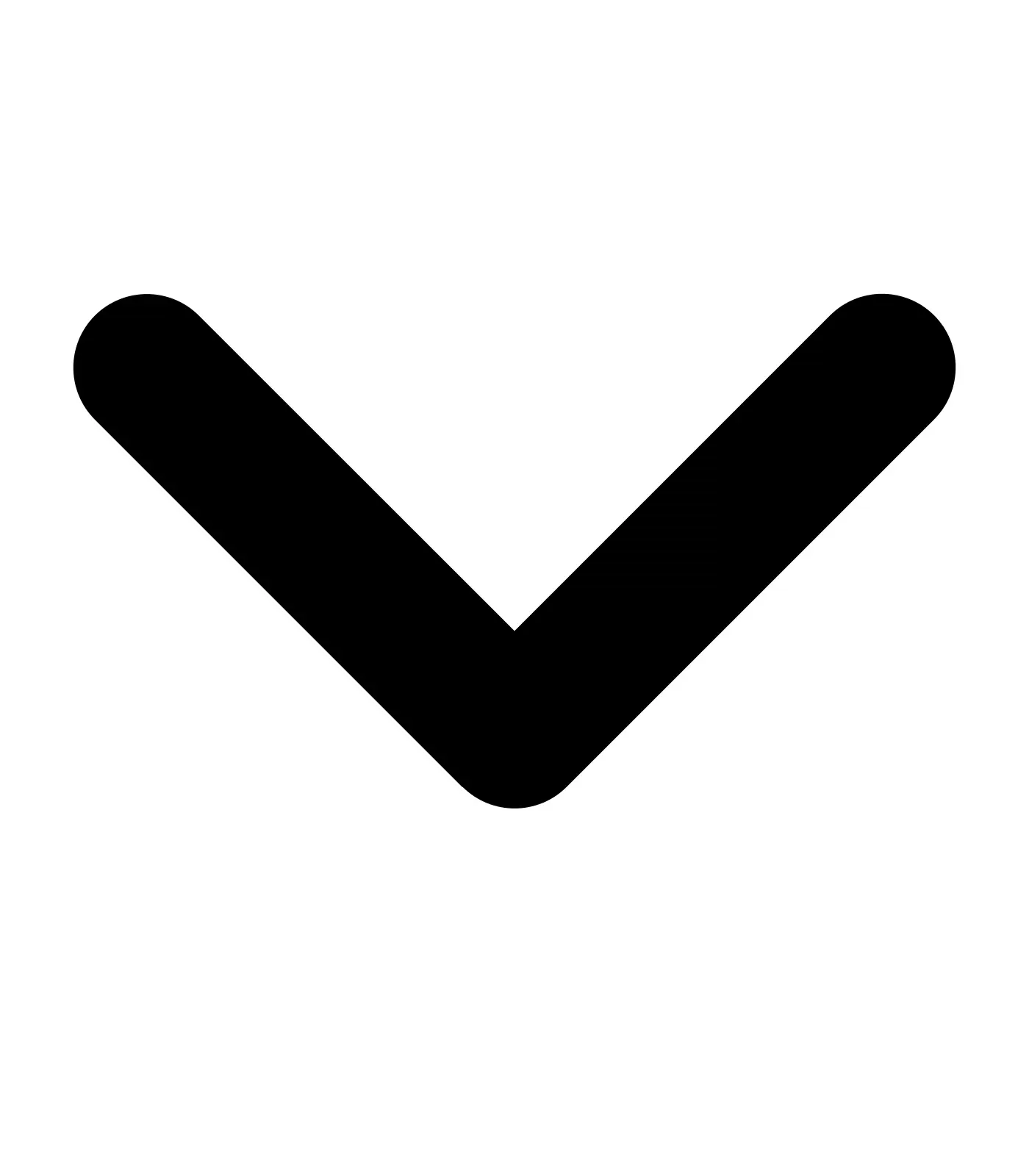
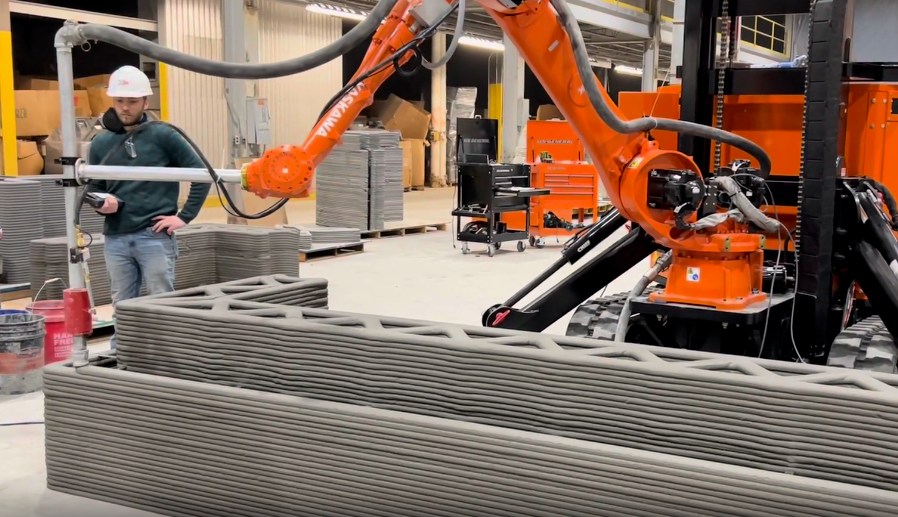
General
3D Concrete Printing (3DCP) also known as additive construction, is a method of building structures layer by layer using a special type of concrete mix. Instead of traditional construction methods that involve manual labor to lay bricks, pour concrete, or place materials, a large 3D printer does the work automatically. This printer, in X-Hab 3D’s case, mounted on a robotic arm, follows a computer design to "print" the designed structure by extruding (squeezing out) concrete in precise layers. It can build complex shapes and structures more quickly, with less waste, and often at a lower cost than traditional construction. This technology is especially useful in areas where it's hard to bring in a lot of workers or materials.
How does 3D concrete printing work?
3D concrete printing (3DCP) is an automated construction method where a robotic printer builds structures layer by layer using a special concrete mix. Admixtures in the concrete control the set time, allowing it to harden quickly without needing formwork. A computer directs the extrusion process, following a digital design to print walls and other elements. This approach saves time and costs while addressing labor shortages by reducing the need for manual labor in the construction process.
Since the Romans, concrete construction has used essentially the same method: forms, reinforcement, mixing, pouring, setting, demolding, repeat. This conventional process is costly, time- consuming, and taking a toll on the environment because of its carbon-intensive makeup.
For the first time in history, builders have an alternative to traditional concrete building. Concrete 3D printing is an automated process that uses stronger, lighter, and more eco-friendly materials. It dramatically reduces build time and material usage while expanding job site safety and design possibilities.
X-Hab 3D’s agile, expeditionary approach reduces the need for site preparation, heavy equipment, and local infrastructure, resulting in significant savings in time and cost. It also enables construction in remote areas where supporting equipment and infrastructure isn’t
available.
X-Hab 3D technology is an integrated ecosystem of hardware, software and printing material. The package includes all necessary components:
- 3D concrete printer with on-board power system, extrusion system, print heads, & material feed system
- Software for design & printing instructions
- Non-proprietary concrete mix (optional)
- Spare parts kit, instruction manual, setup, training, safety gear, & tech support
3D concrete printers range in weight from about 12,500 lbs. for X-Hab 3D’s mobile robotic arm-style printer, to more than 40,000 lbs. for Black Buffalo’s NexCon printer. X-Hab 3D’s mobile 3D printer along with mixer, pump and silo fits on a flatbed trailer or in a 20 ft. shipping container.
Building with 3D concrete requires a system that carefully accounts for material stability, flow, and deformation. Poor results have historically been a byproduct of the printer manufacturer offering bare-bones training.
X-Hab 3D purchases include a comprehensive hands-on training program and 24/7 tech support. And because our system is integrated, it’s easy to monitor for issues on your own and to adjust in real time.
The Printing Process
A robot arm-style printer can be either fixed or mobile. Its print range is defined by the reach of its extendable arm vertically and below grade, but unlimited horizontally when fitted with a mobile track system. It also has 6-axis movement, which enables it to print complex geometries.
The print area of a gantry-style machine is limited to inside the gantry frame. It lacks the flexibility to print complex geometries.
Because X-Hab 3D's robotic arm printers arrive at the job site fully assembled, setup time is hours, not days.
Setup and disassembly of the gantry-style printer on-site is far more complex, labor-intensive, and time-consuming.
A robotic arm-style printer needs only a forklift to load the silo with construction material. A water source and diesel fuel must also be available.
A gantry printer requires a heavy-lift crane to set up and disassemble the gantry frame. It also requires a cement truck to pour the foundation, plus anchor pads for stabilizing the gantry frame prior to setup.
Very.
X-Hab 3D’s mobile robotic printer arrives at the construction site fully assembled. It takes two people about 1 hour to set up and test the system.
The setup process includes: connecting the mobile printer and material feed system, loading the silo with the concrete mix, connecting the water and positioning the printer, then starting the print process.
Material
We can customize the concrete mix’s strength to your requirements. Our 3DCP mixes, and those sold by 3rd parties, have a range of compression strengths from 3,000 to 10,000 pounds per square inch.
Additionally, we’ve engineered the X-Hab 3D system’s print patterns to be more structurally stable than poured concrete.
A primary focus of X-Hab 3D is development of low-carbon, eco-friendly construction material that uses locally sourced and/or recyclable resources for the aggregate.
X-Hab 3D’s concrete mixtures are a blend of sand, gravel, and other locally sourced materials, along with cementitious additives. We engineer your material to meet or exceed the compression, tensile, and flexural strength requirements for the structure.
X-Hab continues to develop lighter, stronger, more flexible, more durable, and more sustainable materials.
X-Hab’s focus is to ensure customers can use local, nonproprietary materials. This keeps costs down and reduces the impact of supply chain variability.
If you’d like, X-Hab can source the materials for you. X-Hab 3D is developing its own sustainable admixtures to enhance concrete properties for your particular project needs.
Yes! X-Hab 3D printers are compatible with a wide range of 3D-printable concrete mixes. We can help you evaluate options.
River sand has a round shape that enhances flow of the blend. Manufactured (crushed rock) sand has sharper angles to its shape, but the system can still use it.
X-Hab can work with you to determine the most effective option.
Quality
Expect a printed home to last as long or longer than standard concrete masonry unit homes, which last about 100 years. The homes are built to International Building Code structural standards.
X-Hab 3D’s robotic printing system is engineered for challenging environments. While conditions like temperature, humidity, and terrain can influence construction, these are managed with specialized admixtures and protective measures like shelters to regulate moisture and temperature. The system's continuous-track platform navigates uneven terrain, while its precision positioning ensures millimeter-level accuracy.
Buying a Printer
Our mobile 3D concrete printing system is designed for commercial and government (civilian and military) applications, from residential and non-residential construction in urban and suburban settings, to mining or oil and gas facilities in remote locations, to military bases in challenging environments around the world. Our focus on sustainable building materials and advanced automation solutions positions us to serve diverse industries needing rapid, resilient, and adaptable construction methods.
Yes, we provide a rental option. You’ll still get the same, complete service and support package as purchasing customers. Contact us for pricing details.
The price of X-Hab 3D’s concrete printing systems varies depending on the specific model and configuration. Contact us for a customized quote and to learn how our systems can enhance your construction process.
X-Hab 3D’s concrete printing system offers a compelling return on investment by reducing material costs by 40-60%, cutting labor expenses by up to 70%, and accelerating project timelines, adding valuable weeks to your schedule. These savings translate into faster project completions, lower operating costs, and increased productivity.
Additionally, buildings printed with our system benefit from superior energy efficiency, weather resistance, and durability, which further reduce long-term maintenance and energy costs for owners. Overall, the ROI for our system not only improves your bottom line but also enhances the quality and sustainability of your projects. Contact us for a detailed cost-benefit analysis tailored to your specific needs.
Support
No – that’s where you come in! However, we offer printing and technical services to builders and construction firms who don’t want to develop them in-house.
X-Hab 3D printing systems come with our complete training program, covering:
- Safety protocols
- Design and printing software
- Material choice & mixing
- Equipment setup, operation and cleaning
- Printing techniques
- Multiple start-to-finish hands-on printing sessions
- Storage & maintenance
- Troubleshooting
X-Hab 3D provides 24/7 technical support for its customers. We can remotely access your sensor and camera data, working virtually in real-time with your field crew to pinpoint a solution within minutes.
We support customer building code requirements as much as possible, particularly when you use our construction material and design-and-engineering plans.
Most building codes are established and enforced at the state and local levels, varying from one jurisdiction to another. We recommend that you find a local structural engineer to work with regulators from the project’s outset to ensure your plans align with code requirements.
Any Other Questions?
Before you take a big step toward scaling your building operation, get all the facts about concrete 3D printing: